Blog-News
Quality Parts and Service – Ensuring Maximum Performance of your Lancaster Mixer
Lancaster Products has been the industry leader for mixing and material handling solutions for more than 30 years. Because Lancaster Products are built to last, our commitment to our customers extends well beyond the warranty period. We place an emphasis on keeping our customer’s machines running well with our factory genuine spare parts and maintenance services.
Lancaster Products Genuine Parts
The failure of component parts can cause costly disruptions and delay production schedules. Lancaster Products provides a full array of factory genuine replacement parts specifically designed and specified for the Lancaster Machine. All Lancaster Products parts must pass stringent quality requirements to ensure high performance standards. Using Lancaster Products genuine spare parts and services avoids problems such as premature failure and lower performance that might be experienced with a third-party part.
Effect of Mixing Intensity on Mixing time
Industrial mixers are often considered the heart of a processing facility. While we at Lancaster Products are diligent in our up-front materials processing sampling, it is not enough to simply confirm that the required physical specifications of the materials are met.
When choosing an industrial mixer one must understand that there are a significant number of factors that need be taken into consideration such as yield rates, cost per yield, mixing time, mixing intensity, etc. It is critical that machine builders have a complete understanding of the entire process to recommend the right mixer to maximize the overall processing workflow
Use of High Shear Mixers for Refractory Applications
Refractories are important to high temperature manufacturing for their thermal insulation properties and are commonly used to protect personnel and equipment. They are critical to industries such as glass, ceramic, and metallurgy. In general, refractories are used for temperatures in excess of 2,000°F, for applications such as the melting of glass or metal, or the curing of ceramic wares.
Alumina (neutral) and magnesite (chemically basic) represent two common ingredients used in the production of refractories, which involves a mixing step which is critical to the quality and cost of the final product. Mixing is critical because raw materials can be vastly different in physical characteristics, such as particle size (from powdery to 1/4” granular) and bulk density (35 pcf for graphite to 100+ pcf for minerals).
Perfecting Mixing and Pelletizing in the Lancaster Products Laboratory
Quality products start with quality materials. Lancaster Mixers improve material processing and achieve better results than conventional mixing or pelletizing machines in a single machine and process. Exploring how to achieve better material results starts in the Lancaster Products laboratory. Whether our customers are looking to improve an existing process, or define a new method for processing materials, the high shear mix design for producing the end product is iterative. It starts as a proof of concept, and scales up to a production mixer run along the way refining the optimal mix program. Many Lancaster customers consider the process through a K-series high shear mixer the secret catalyst to make their products extraordinary and give them an advantage in an ever more competitive marketplace.
Buying a key piece of equipment without knowing exactly how it will perform is a risky proposition, so Lancaster Products will work hand-in-hand with clients to establish a level of comfort with the K series mixer before ever committing to a purchase order. For a small investment in time and money, Lancaster Products provides a complete scope of testing services. This important activity allows our customers to hit the ground running with an established mix design and knowledge on mixer operation.
Advantages of Pelletizing in a Lancaster Mixer
We are often met with skepticism when informing prospective customers that Lancaster Products’ high shear “mixers” can actually pelletize materials more efficiently than the “pelletizers” they either currently use or are considering for use in their materials...
Pelletizing Carbon Black Using High Shear Mixers
Everyone remembers from grade school that if you mix a bunch of colors together you get black. But in the world of manufacturing and mass production making products black isn’t so simple. Black pigments that satisfy specified requirements must be used to achieve the desired color, and when it comes to making black pigments, there’s no better place to start than the residual by-product of refineries appropriately known as “Carbon Black”.
Challenge: In its raw form, carbon black is a very fine powder, so fine that it has liquid-like properties which makes it difficult to handle when transporting between and within facilities. It is also classified as a Group 2B carcinogen and becomes airborne easily when in its raw, powder form.
Background: Carbon black is a waste product generated in large volumes by petroleum refineries around the world. Rather than dispose of it, refineries will opt to sell it to materials processors who process it so it can be incorporated into pigments and fillers with a wide variety of uses, particularly in the steel, rubber, and plastics industries.
Converting carbon black powder to a pelletized form significantly reduces the risk of releasing carcinogens into the air when handling. The pellets are also much easier to store and transport due to the lower flow rate of pellets vs. powder.
Lancaster Products Now Offers Equipment Financing Through a Partnership with First National Bank
Lancaster Products has partnered with First National Bank Commercial Leasing (FNB) to offer flexible financing terms on Lancaster Mixers and equipment. We can structure a variety of options for installment payments, capital leases, operating leases or rent to own. ...
High Shear Mixer Rentals for On-Site Testing and Processing
Lancaster Products offers a unique and valuable High Shear Mixer Rental Program for materials processors who are considering the purchase of a high shear mixer to satisfy their production needs. Rental mixers allow customers to try out the Lancaster Mixer in their own facility to determine if it is the right equipment for the customer needs before making an investment to purchase. Rental mixers allow for an extended testing period and play a critical role in defining required specifications and fine tuning the process to improve performance for outcomes such as increased yields, reduced mix times, reduction in additives, and overall increases in efficiencies. Moreover, rental mixers are an excellent, cost effective way to compare results of existing equipment lines against a Lancaster Mixer to determine performance improvements and calculating Return on Investment with real world data.
How does short term rental equipment solve the need for long-term continual processing applications? The methodology behind the science of materials processing closely follows the scientific method: start with a hypothesis–>test it–>observe and record–>modify–>test–>repeat until the final result is reached. As a result, the majority of new projects presented to the Engineers at Lancaster Products must be proven in physical testing before they are ready for mass production, which means our involvement goes beyond taking the order for a mixer and manufacturing it to meet the mechanical specifications. Most projects start with small batch testing in a K1 Mixer at the Lancaster Products testing facility. This is where theories are proven and formulations are developed. But, scaling up from small batch processing to large production runs doesn’t necessarily follow a linear scale so additional testing in a production sized mixer is recommended.
Lancaster Products High Shear Mixers Make Glass for LCD Screens Used in Electronics
If you’ve ever watched a flat-screen television or used a smart phone there’s a good chance the glass showing the picture was made by machinery developed and produced by a Lancaster Products high shear mixer in Lebanon, Pennsylvania.
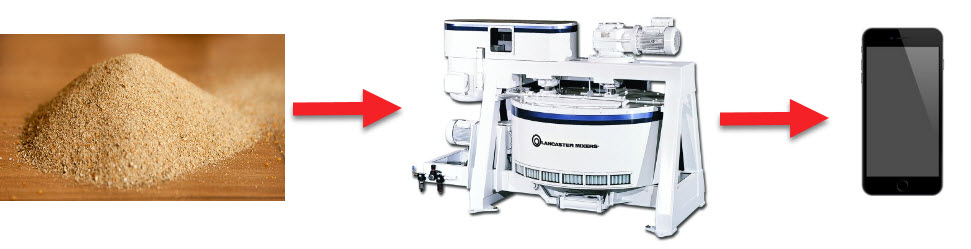
Image for illustration purposes only
New Ownership at Kercher Enterprises
After 70 years as a family business, Kercher Enterprises is pleased to announce new ownership as of April, 2016. Curt Snyder purchased Kercher Industries (www.kercherindustries.com) and the Lancaster Products (www.lancasterproducts.test) brand of high shear mixers. Additionally, he assumes the role of President and CEO. Previous owner, Ed Kercher will remain on staff to share the wealth of knowledge he accumulated since his family started the business in 1946. Current and future customers can expect the same great service and dedication to excellence that has become a trademark of Kercher Industries and Lancaster Products.
Curt has served in numerous financial and operational roles over his 20 year professional career including as a management consultant for Accenture and successfully leading Mergers and Acquisitions for companies such as Triumph Group and QuEST Global Services. This experience provided Curt with a good eye for identifying healthy companies with growth potential and an understanding of how to best manage the transition. Kercher Enterprises perfectly fit his search criteria and fulfilled Curt’s goal of owning his own corporation. Says Snyder, “Kercher Enterprises stood out among the other manufacturing companies I looked into, because of the positive impact it has on its customers in delivering value and solutions. Customers come to us every day with new challenges that require our expertise and that keeps me and my employees excited to come to work every day.”
